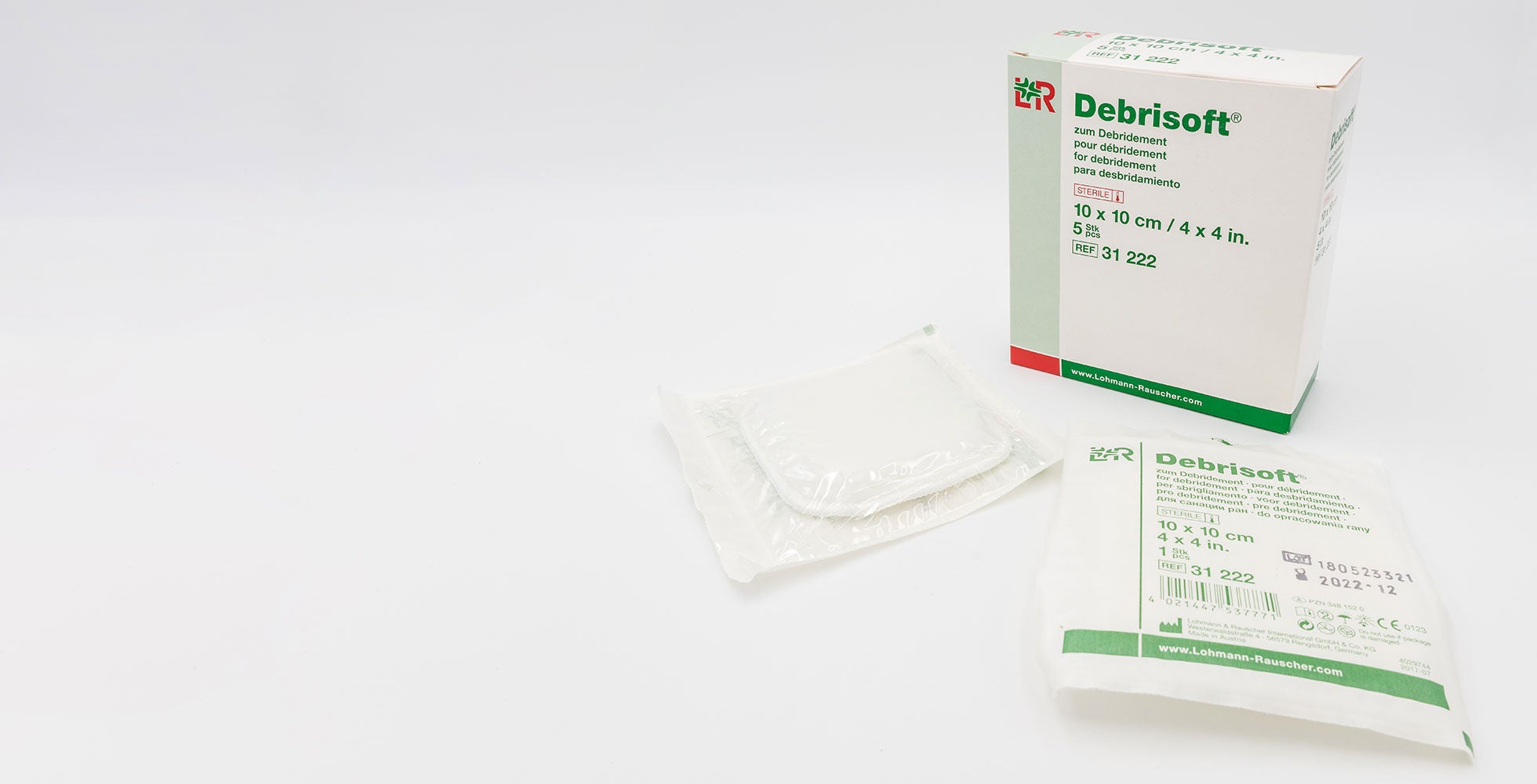
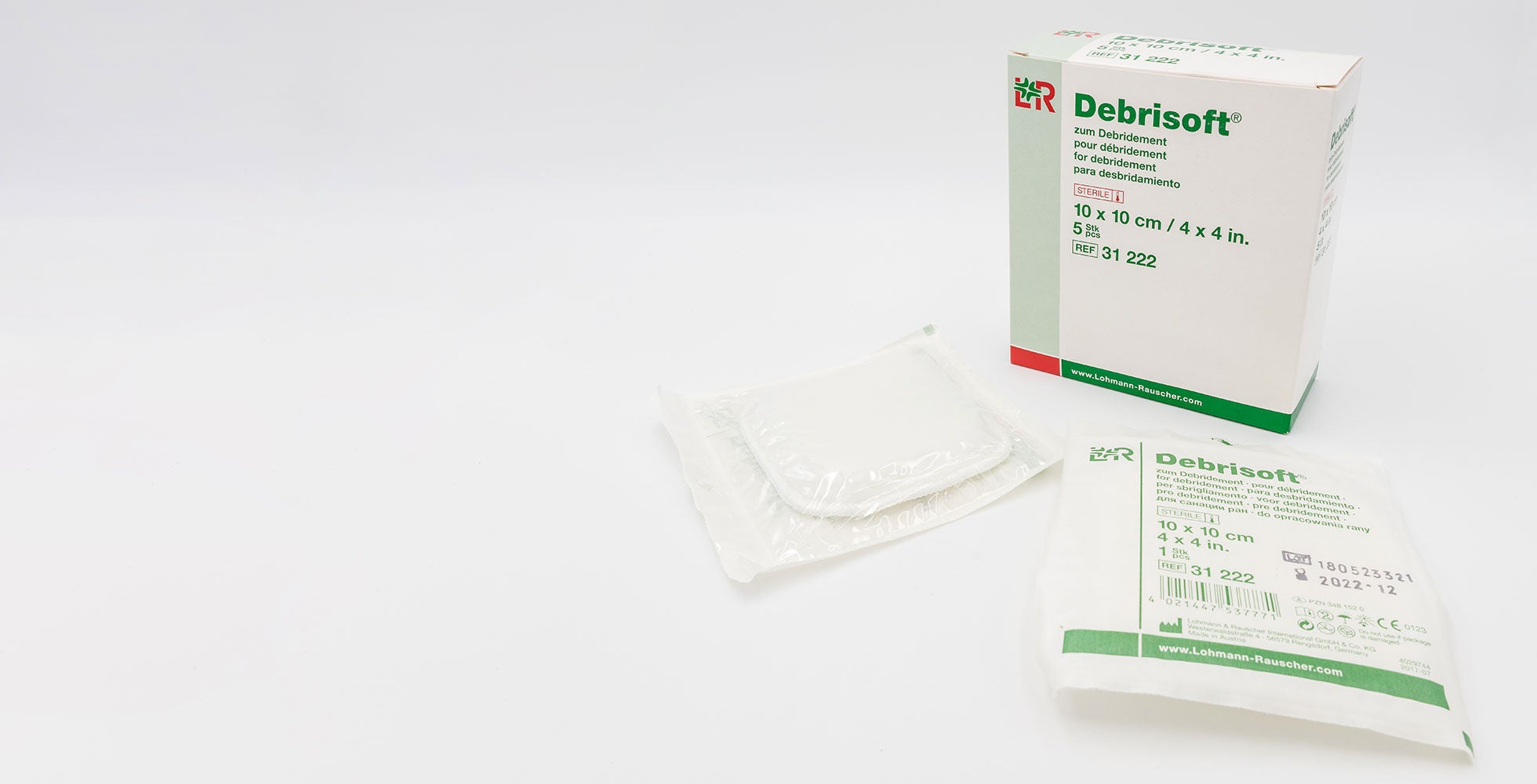
The company was formed in 1998 by the merger of the two traditional companies, Lohmann Medical and Rauscher. When he founded the company “Handlung in Material-Waren” in Frankfurt am Main in 1851, Julius Lüscher laid the foundation for the Lohmann company. The Rauscher company, which was founded in 1899 in Vienna, developed within a short period of time into one of the leading suppliers of bandages and hygiene products for nursing care in the Austro-Hungarian Empire. Following the merger, the headquarters of both companies were retained in Rengdorf in Germany and Vienna in Austria. The internationally operating company currently employs around 4,000 and generates an annual turnover of some 600 million euros.
A clean wound is essential for the healing process. Thanks to Debrisoft® from Lohmann & Rauscher, nursing staff in hospitals, outpatient services, and medical practices have reliable and sterile products available, which have a positive effect on the healing process and therefore quickly lead to visible results. When being used, the soft fibre side of the micro-fibre pad is well moistened with a wound rinsing solution and then lightly wiped in a circular motion over the wound or the skin surrounding the wound. This enables the sloping fibre tips to release dead cellular debris and deposits from the wound, as well as scales and keratosis from the skin surrounding the wound. This ensures replacement tissue (granulation tissue), which regrows during the wound healing process and enables the wound to close quickly, together with the existing epithelial cells are gently protected.
“As far back as 2011, we revolutionised wound management with the introduction of the Debrisoft® monofilament fibre pad, and we further expanded our range in 2015 with Debrisoft® Lolly for deep wounds,” explains Karl-Heinz Posch, Director of Technology and Process Engineering at Lohmann & Rauscher.
The tissue removal pads are packed on a R 245 thermoforming packaging machine. “Since the loading on the existing MULTIVAC packaging machines was already very high, we decided to invest in a new machine with three different die sets so that we could achieve flexible use of the packaging system. Due to the many years of successful collaboration with MULTIVAC, there was only one possible supplier,” explains the Technical Director.
The R 245 thermoforming packaging machine is designed for the demands of the medical products industry, and the operation of the machine is particularly ergonomic and reliable thanks to the HMI 2.0 user interface, which is operated intuitively. As part of the investment project, validation and calibration of the packaging solution at MULTIVAC were also ordered by Lohmann & Rauscher. The packs have to comply with the current Medical Device Regulations (MDR) as well as ISO13485, ISO11607 and the FDA regulations.
The R245 was also equipped with a discharge conveyor for the synchronised discharge and converging of the packs. The thermoformed pack is produced from a flexible lower web and an upper web of medical paper. The gas permeability of the paper enables the packed products to be sterilised with ETO (ethylene oxide). “As we had expected, putting the packaging solution into service and validating the process went like clockwork,” confirms Karl-Heinz Posch.
Since the products come into direct contact with wounds, the sterility of the products is of the greatest importance. Particularly important for the company was therefore the quality of the seal seam, which is achieved by an even distribution of sealing pressure and temperature during the sealing process – as well as by reliable monitoring. If, for example, the machine stops, it automatically checks how long the film was under the heating plates in the forming and sealing dies. If the time is exceeded, the pack is “marked as reject”. Since reject packs are not cross cut, they can be easily detected by the operator and removed immediately. If the sealing pressure is not reached, the affected packs are similarly rejected.
A thermal transfer printer from a third-party supplier is used for the product-specific inline printing of variable data such as LOT number and use-by date on the pre-printed material. This printer was integrated by MULTIVAC into the packaging line.
According to Karl-Heinz Posch, the machine and printing system had to be put into service very quickly, because “the product sells very well and we wanted to start the production and packaging procedure as quickly as possible.” Everyone is very satisfied with the pack quality and the thoroughly professional collaboration.
10.06.2018