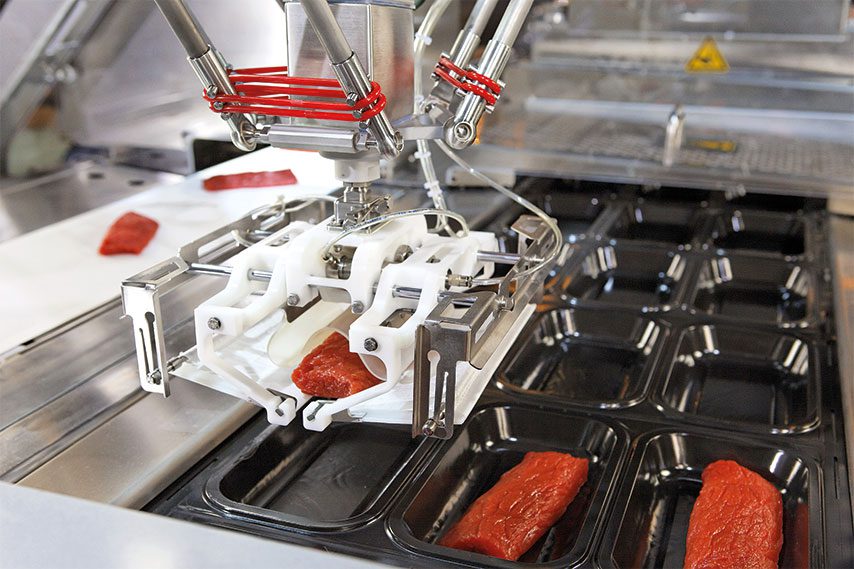
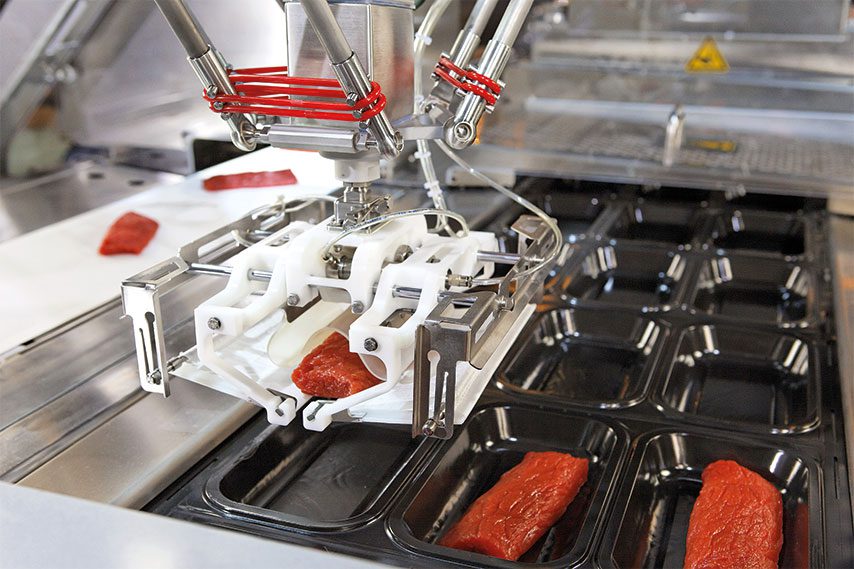
Compared to other sectors, the food industry overall still has a relatively low degree of automation. Only around three percent of all robots sold every year are supplied to the food industry. The largest and fastest growing market for robots is the automotive sector with around 100,000 industrial robots sold per year, followed by the electrical and electronic sector, the metal and chemical industries, as well as the plastics industry.
The main cause of the very subdued rise in the degree of automation in the food sector lies with the products that are processed: here it is a case of natural and often delicate products, which can spoil very easily. The packaging procedure in all its different parts has to be tailored individually to the product, its shape and its specific characteristics. It is therefore very difficult, or in many cases barely possible, to standardise the procedure.
When production figures rose in the past, it was generally the case that more machines were used, larger or additional production facilities built, and more people employed for the various tasks and inspection duties. Today it is incomparably more difficult to find suitable personnel. Particularly if less attractive or repetitive tasks are involved. It is for this reason that nowadays not only larger companies but even smaller ones are faced with the question, how they can meet the daily requirements efficiently, and above all cost-effectively.
Lack of personnel is however not the only factor causing companies to strive towards a higher level of automation. Rising personnel costs due to the intense competitive situation, together with the introduction of minimum wages, are having an immense impact. These rose to 160 percent in the years from 2000 to 2015 alone. In the same period the selling prices to food retailers could only be adjusted upwards to a limited extent. An additional aggravating factor are the ever stricter hygiene requirements, which are prescribed by EFSA (European Food Safety Authority), the American FDA (Food and Drug Administration) and the IFS Food Standard, which is a standard recognized by the Global Food Safety Initiative for auditing food manufacturers. And last but not least, the demands placed on the product are also increasing, such as sell-by dates, traceability, and product marking.
Automation is a productive approach to all these challenges. Even where delicate products in the meat and sausage sector are involved, the possible areas of use for automation solutions within the packaging procedure extend from product infeed and loading right up to pack inspection and secondary packaging or palletising at the end of the line. Automation is however only sensible, if the degree of automation is tailored to the needs of the company, and is economically viable. And if above all the human element in the process can be replaced completely. The location, at which the largest number of people are employed, is not always however the best place to integrate automation components.
One part of the process, which can certainly be automated sensibly, is monitoring and inspection of pack or product. If the human element was previously the “measure of all things” when it came to inspection of product, packaging or labelling, it is now practically impossible to perform reliable inspection at high output in this way. Individual random sampling is also generally insufficient to meet the statutory requirements and ultimately guarantee consumer safety. This is because the requirements are very complex, particularly in the food industry. The product and packaging have to be subjected to reliable checking for foreign bodies, often at very high throughput. When it comes to checking quality, it has to be ensured, for example, that the packaged meat does not display undesirable characteristics, that the right number of sausages have been loaded into the pack, or that the ham slices are correctly arranged in the thermoformed pack.
When it comes to labelling, there are also many possible sources of faults: Is the label applied in the correct position? Was it even applied? Is the barcode legible? Does it contain all the relevant information? Was the correct best-before date given? Does all the information correspond to the reference data stored in the system? In order to ensure only correct packs get into the retain chain, each individual pack has to be checked. This task can only be performed quickly, accurately, and reliably by automatic inspection systems. As a labelling and marking specialist, which covers the entire spectrum of solutions for inspection tasks, MULTIVAC can offer a comprehensive product portfolio, ranging from inspection of label presence and position (label, print image, product) right up to character recognition and verification (OCR, OCV), legibility and content analysis of one- and two-dimensional codes, and even pattern recognition. The inspection solutions can be integrated directly into the packaging line or designed as stand-alone solutions. Among the most frequently used inspection systems are simple sensors, barcode readers, vision sensors, and intelligent camera systems.
It is not only inspection, where automation pays off, but also in the process stages upstream and downstream of the packaging machine. In most cases these are repetitive tasks, but also difficult tasks that can not be performed ergonomically. Examples of these would be loading meat or sausages into the pack, or loading primary packs into secondary packaging and then stacking the boxes on a pallet. But even though these areas are highly suited to automation, a certain degree of flexibility is required whenever natural raw materials are being processed.
One company, which has to pack very flexibly, is Radeberger Fleisch- und Wurstwaren GmbH. Here, highly efficient and user-friendly packaging machines and automation equipment from MULTIVAC have been used for around 25 years. There are now a total of eight systems in operation, including a sausage loading robot, which places each of the more than 30 types of natural casing sausage cleanly and precisely into the pack cavity, and all this at high output and always in the required quantity. In order for the H 240 handling module to easily grip the different sausages, they are sorted and separated on a special infeed conveyor.
The packaging procedure for sliced products is also highly suited to automation. Here, various different handling modules within the packaging line can make a very significant contribution to a more efficient and hygienic procedure, since the human element is still the greatest hygiene risk when sensitive meat products are being packed. At this years’s Anuga FoodTec MULTIVAC exhibited a complete line for packing sliced products, and in comparison with conventional solutions on the market, this line has a significantly reduced footprint. The MULTIVAC solution incorporates the compact and flexible R 245 thermoforming packaging machine, equipped with the Horizontal Loader, a loading system for sliced products that is hygienic and gentle in its handling. As an alternative, a high-performance pick-and-place robot can be used, which is similarly designed to load sliced products reliably and hygienically into the packs at high output.
Another application for industrial robots is where one or several food packs at a time are picked up and placed in a uniform or offset pattern in a secondary packaging box or reusable
container. In addition to this, these secondary packaging boxes can also be easily palletised with a handling module. Depending on the size of the production room, required functions and desired output, the modules can be equipped individually with 2-, 3-, or 4-axis robots and appropriate gripper systems. They can be used very flexibly for a wide variety of products, pack formats, weights, and cycle times, and they meet the requirements of the food industry thanks to the MULTIVAC Hygienic Design™.
But it is always a case of carefully analysing the particular circumstances, defining the requirements and applications, and then developing a solution in conjunction with the customer and his specific needs. This can only be achieved by those companies within the industry, which have
experienced staff and the necessary product portfolio.
When seen overall, handling modules can therefore take over a large number of tasks in many areas of the packaging procedure, which were previously carried out by a person. When it comes to process reliability, hygiene, efficiency, and cost-effectiveness, the use of a robot is beyond dispute. Packaging material can also be reduced, since with the aid of automation a smaller pack can often be designed, thus saving material.
As with the lower personnel costs, the reduced use of plastic when packaging the meat or sausage product also has a positive visible effect. This is also a very productive step given the amendment to packaging legislation, which is due to come into force from 2019, and the EU Plastics Strategy, which requires a significant reduction in the use of plastics, as well as improved recyclability of the materials used in the packaging industry.
On this topic of packaging material reduction, there are many other solutions available. In addition to innovative cutting systems, such as the BAS 20 cutter from MULTIVAC, which can be used on all thermoforming packaging machines and can be designed to cut without film trim, the focus is also on modern packaging technology such as MultiFresh™ or shrink packs. These allow packaging material to be saved without adversely affecting the stability or protective function of the pack.
MultiFresh™ is a packaging system for high-quality vacuum skin packs, which protect both solid and soft food products without deforming them. The highly transparent upper web is completely draped over the product like a second skin, and it fixes the product in place within the pack, allowing it to be presented at the point of sale either standing up or hanging, as well as lying flat. The high-quality skin films have outstanding mechanical properties, which means they can be used as a sub-
stitute for thicker materials.
In the case of shrink packs and in particular with the MULTIVAC FormShrink™ process, the product is packed in a special shrinkable film. The shrink properties of the film are activated by brief contract with hot water. Both packaging methods reduce material consumption significantly - and therefore also the costs.
The full potential of a higher level of automation can only be fully exploited as regards efficiency, process reliability, cost-effectiveness, and ease of operation, if all the modules are integrated into the machine control and can be managed via one single control terminal. In MULTIVAC packaging lines the higher-level MULTIVAC Line Control (MLC) links all the components in the customer’s packaging line, and it coordinates these right up to the ERP system. This ensures precise, reproducible, and transparent processes are achieved - and it requires only the minimum of operating staff.
Whereas up to now all the specific parameters and configurations also had to be set on the individual line components, such as handling modules and inspection or labelling solutions, and all these settings had to be changed over to the new product during a product change, higher-level recipe management enables the settings for the individual line components to be linked in the form of sub-menus to the main recipe, which is called up on the packaging machine. When the recipe for a certain product is called up, each line component is automatically sent the message by the HMI, that the corresponding sub-menu is to be called up. The packaging procedure is therefore simpler, faster, and more efficient - and can also be controlled reliably by staff with only brief training.
It must also generally be the aim with a largely automated packaging solution to reduce the footprint of the complete system to a minimum. An automated packaging system should not take up more space than a conventional packaging solution. This can only be achieved successfully, if the packaging machine is part of the automation solution, and all the automation components, such as for example with the slicer solution, are integrated intelligently.
24.09.2018