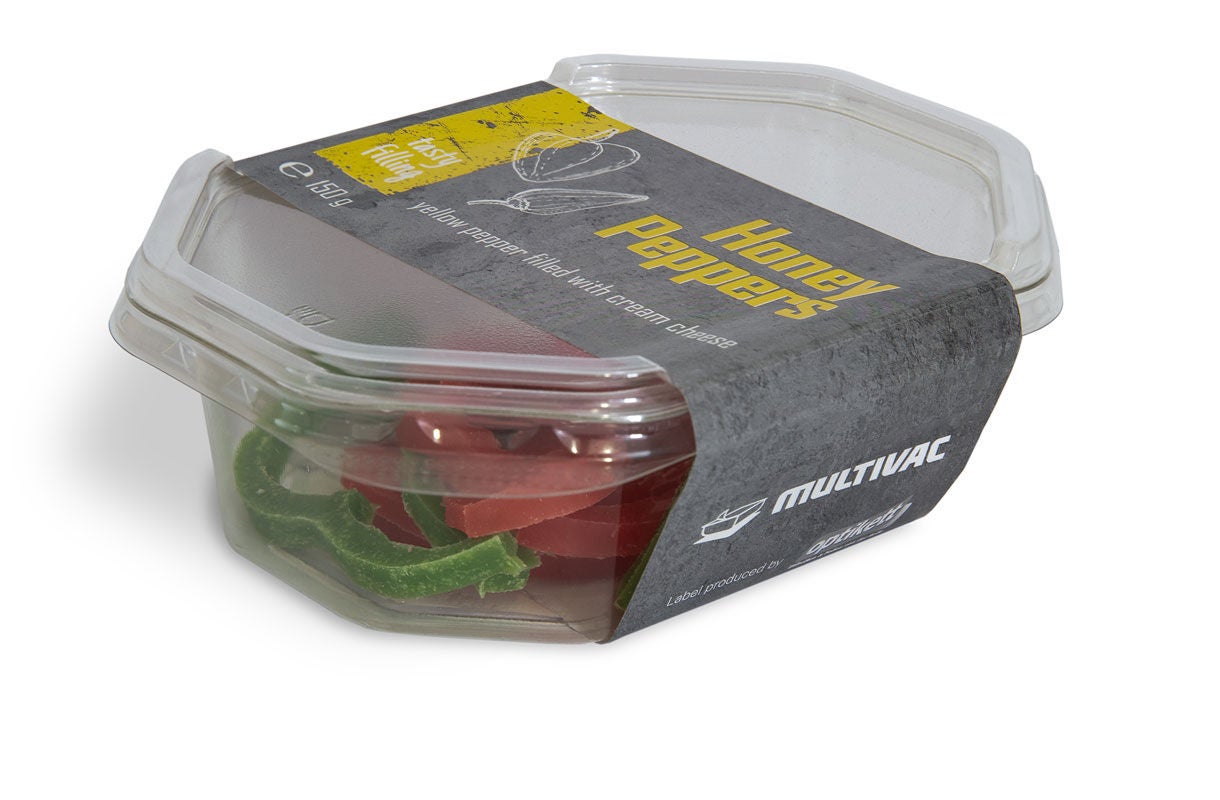
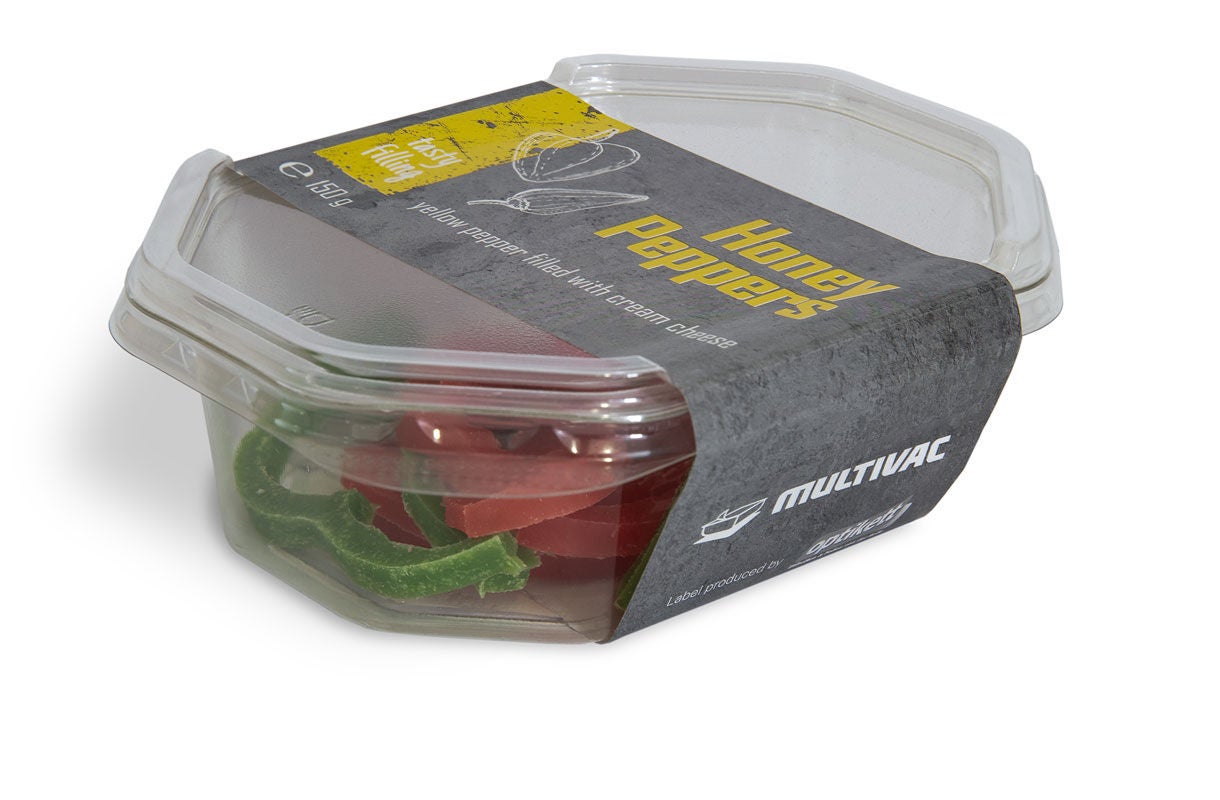
Thanks to their modular design, MULTIVAC’s conveyor belt labellers offer a high level of flexibility for labelling a wide range of packs, such as pots, jars, bottles, folding cartons, tubular pouch packs, thermoformed packs, trays, and even boxes. They can be integrated seamlessly into new and existing filling or packaging lines, or they can be used as a stand-alone solution with manual product infeed. The conveyor belt labellers are also very flexible as regards the positioning of the label on the pack. Labels can be applied to the top or bottom of packs, to one or more of their sides, as well as on the leading face or over the edges of the pack. MULTIVAC also offers, as equipment options, a wide range of transport conveyors, applicators, printers, and visual inspection systems for many different applications and requirements.
MULTIVAC conveyor belt labellers also offer users many benefits, including the complete integration of printers into the control interface of the labeller. This makes it easy to configure the printer parameters as well as assigning and automatically loading the print layouts from the MULTIVAC recipe. Operating errors can be prevented almost entirely, while downtime is reduced and batch changes can be handled more quickly. The integration of inspection systems for checking label print and presence also contributes to greater reliability of the labelling and packaging procedure.
An important application for conveyor belt labellers is the D labelling of packs. D labelling, which is also known as “full-wrap labelling”, is understood to mean the labelling of packs on four sides, since the label is completely wrapped around the pack, similar to a sleeve or banderole. Thanks to this, D labelling offers many possibilities in the design of the pack, and this in turn contributes significantly to increasing the attractiveness of these packs at the point of sale.
Due to the extensive system of modular construction used by MULTIVAC, solutions for D labelling can be offered, which are designed very flexibly for a wide range of pack shapes and materials, and this means the optimum labelling result can always be achieved, even when there are frequent changes of pack shape or design. A typical application are skin packs with different heights of product protrusion. Since unprinted upper webs are mostly used on skin packs, the label plays an important role with these packs in distinguishing the product. D labelling is also used on MAP thermoformed packs or trays in a wide range of shapes, such as salad packs.
MULTIVAC’s labelling solutions offer users a high degree of automation, as well as maximum labelling accuracy. If required, the conveyor belt labellers can also be equipped with extra label dispensers, so that additional labels beside the full-wrap label can be applied to the pack. One example of this would be promotional labels, which are increasingly being used for packs on the fresh food shelves.
When one considers the range of label materials, which can be run on MULTIVAC labellers, there are virtually no limits in terms of the nature and thickness of the materials or the shape of the labels. In addition to their function as an information medium, full-wrap labels are increasingly becoming important design elements in retail packs and an attractive alternative to more elaborate sleeving solutions.
With its L 310 labeller, MULTIVAC offers a robust and low-maintenance conveyor belt labeller for higher outputs and more complex labelling, printing, and inspection requirements for a wide range of packs. This model with its modular design is equipped with a servo-driven press-on unit for full-wrap labelling. This enables label lengths of up to 500 mm to be run. The controls for the
L 310 can be integrated into the machine control of the packaging machine, and the label dispenser is adjusted in height very ergonomically from the front of the unit. This very versatile model can also be equipped with a compressed air operated blow-on applicator, which is used to apply promotional labels without contact to delicate products or into the base of skin packs.
The use of so-called “linerless” labels, which do not require a carrier material, is an alternative method of full-wrap labelling. This means there is no waste carrier material during the labelling process. Due to the reduced material thickness, the label rolls have longer running lengths and therefore have to be changed less frequently.
“But if one looks in greater detail at full-wrap labelling with self-adhesive labels, one sees that self-adhesive labels offer significant benefits over “linerless” labels, since they increase the efficiency of the labelling process, as well as improving the impression of the packs, thereby optimising their attractiveness at the point of sale,” explains Michael Reffke, Product Manager for Labelling Technology & Strategic Product Management at MULTIVAC Marking & Inspection.
The labelling expert also adds the benefits of the greater flexibility of self-adhesive labels when it comes to design and shape. Whereas “linerless” labels can only be produced in a rectangular format, all shapes can be considered for self-adhesive labels, since they are “held” in effect by the carrier paper. Labels with curves or cut-outs for example are possible with self-adhesive labels, which means they can be matched to the shape of the particular product or pack. By using self-adhesive labels, the product manufacturer has far more opportunities to differentiate his packaged product from others at the point of sale. It is the same story with the range of materials, which can be used for the production of self-adhesive labels – this is much wider than for “linerless” labels, since the carrier material for the self-adhesive labels has a stabilising effect on the label material. One can generally assume, that the grammage of “linerless” labels is higher than that of self-adhesive labels, even if they both appear to have a similar feel. This means the number of labels per roll of self-adhesive labels can be up 30 percent higher than that of “linerless” material. This results in a reduced number of roll changes during production and therefore less downtime.
Another aspect, which restricts the efficiency of “linerless” labelling systems, is the fact that running these materials causes increased cleaning work on the machine. Labelling machines for running “linerless” labels also have to be equipped with knives, so the labels can be cut from the endless label stock. Residue of the adhesive or silicone layer on the labels builds up on these knives, which means they have to be cleaned regularly in order to maintain optimum labelling. The machine running time is therefore reduced significantly.
In addition to this, the number of suppliers of self-adhesive labels is many times greater than that in the “linerless” sector, and this in turn creates many purchasing benefits for companies using labels. This also has a positive effect on the cost effectiveness of the labelling solution.
When it comes to disposing of the carrier materials, the leading manufacturers of self-adhesive labels have set up comprehensive recycling programs, ensuring the carrier materials are fed back into the right recycling loop and can be properly recycled.
Another area, where D labelling with self-adhesive labels offers benefits over established systems, is as a replacement for so-called “card sleeves”. A card sleeve is single-piece sleeve, into which the final pack is pushed. These “card sleeves” have a high-quality image and offer the product manufacturer a large surface for graphic design and information, which means they contribute significantly to product differentiation at the point of sale. These “card sleeves” can also be fed back into a recycling loop, and this reduces the carbon footprint of the packaging significantly. Since these “card sleeves” are often however pushed over the packs manually, and since they also require an additional label on the rear to attach the sleeve to the pack, this type of packaging involves significant extra cost when compared with automatic D labelling. D labelling can therefore offer an attractive alternative, particularly when paper labels with a higher grammage are used.
26.03.2018